3D vision comes natural for human beings. With our eyes we all capture the 3D geometry of our environment to walk around and perform a multitude of tasks. The stereo vision of our eyes enables us to estimate the size of objects and how far away these are positioned (depth). A standard 2D camera only captures the intensity or color values of the environment without having pixel-level information related to the depth of the items shown on the image.
Many techniques have been invented to capture depth information from the environment. Subsequently, this depth information can be used to improve the robustness or precision of algorithms that process the image information for a specific application. 3D vision is applied as part of a range of applications in logistics, agriculture, rail, wood and many other markets.
A range of 3D application challenges, in which depth information can be used to improve the robustness of algorithms, is segmentation. The detection of pallets is one of many concrete applications where depth knowledge about the environment is key. With a regular 2D camera it is difficult or impossible to reliably detect the position and size of pallets. 3D vision also captures the depth information, which allows for the straightforward detection of pallets as well as their locations and dimensions.
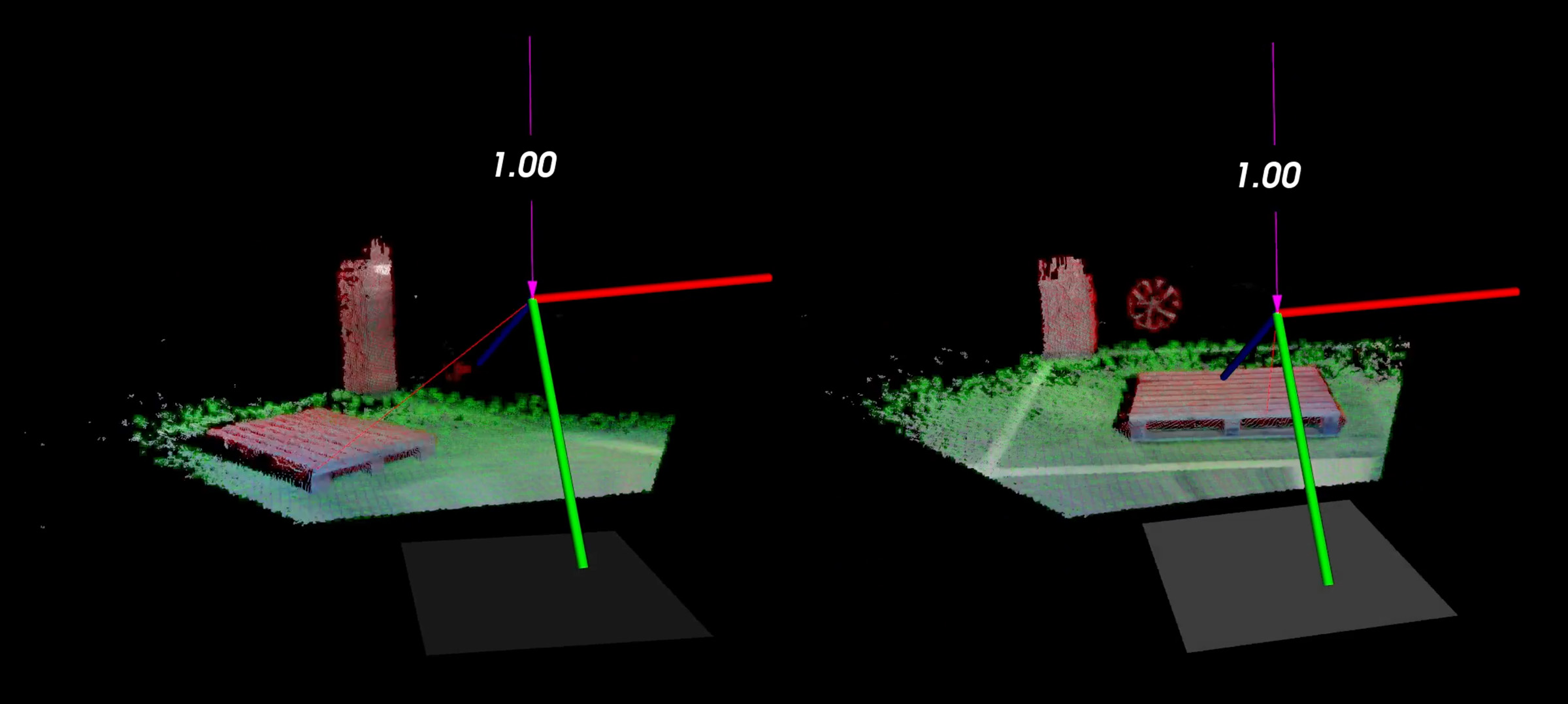
3D vision applied to distribution center challenges
Concretely, APIXA uses 3D cameras and AI software intelligence to monitor the automated process of placing goods on a pallet in a specific order. This enables distribution centers to optimize the supply of the goods to individual department stores. The order of the mixed stacking depends on stores' supply needs and shop layout as well as physical product constraints and legal regulations. APIXA signals product packaging issues throughout the process by comparing 3D images with a theoretical pallet model stacked with corresponding product models. This avoids skewed store deliveries which may potentially lead to harmful situations, material damage or food waste.
Application-dependent 3D vision choices
The success of using 3D vision in an application strongly depends on the proper choice of measurement technology. There is no technique that performs well under all conditions. The following conditions need to be considered when selecting the most appropriate measurement technology:
- Physical properties of the environment (e.g. material properties, texture)
- The available time to execute the measurement
- Potential movement of the setup and the environment
- The desired accuracy and image resolution
- The dimensions of the object that needs to be measured, and potential occlusions
3D vision comprises of different technological approaches that add the depth information, including triangulation, structured light, time of flight, and stereo vision. Lidar, for example, is a special combination of 3D scanning and laser scanning.
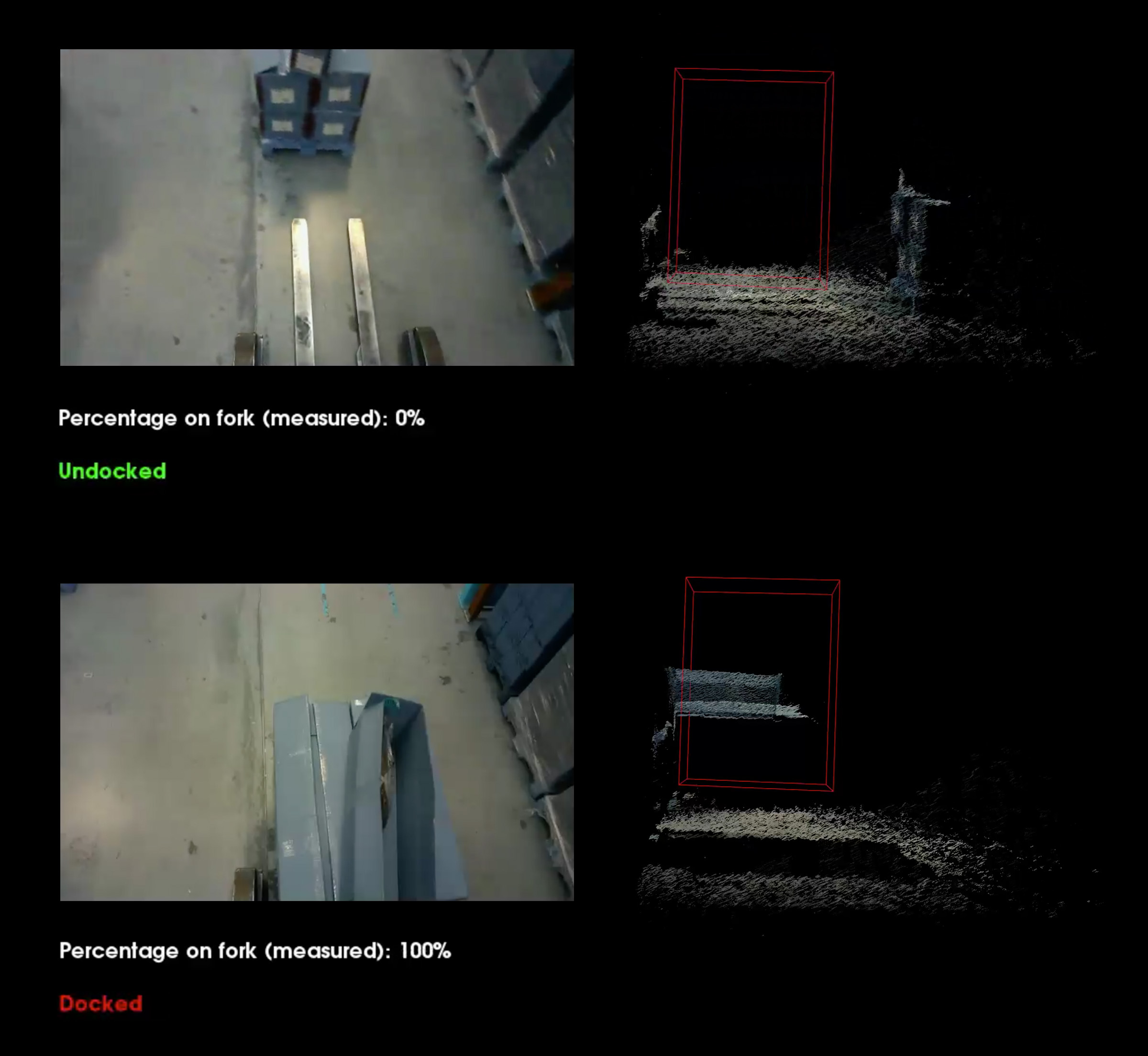
Software supporting 3D vision performance
Software also plays a critical role in making better use of 3D vision in specific applications. By tailoring software around the selected measurement technology, the robustness and speed of dealing with specific artefacts can be increased considerably.
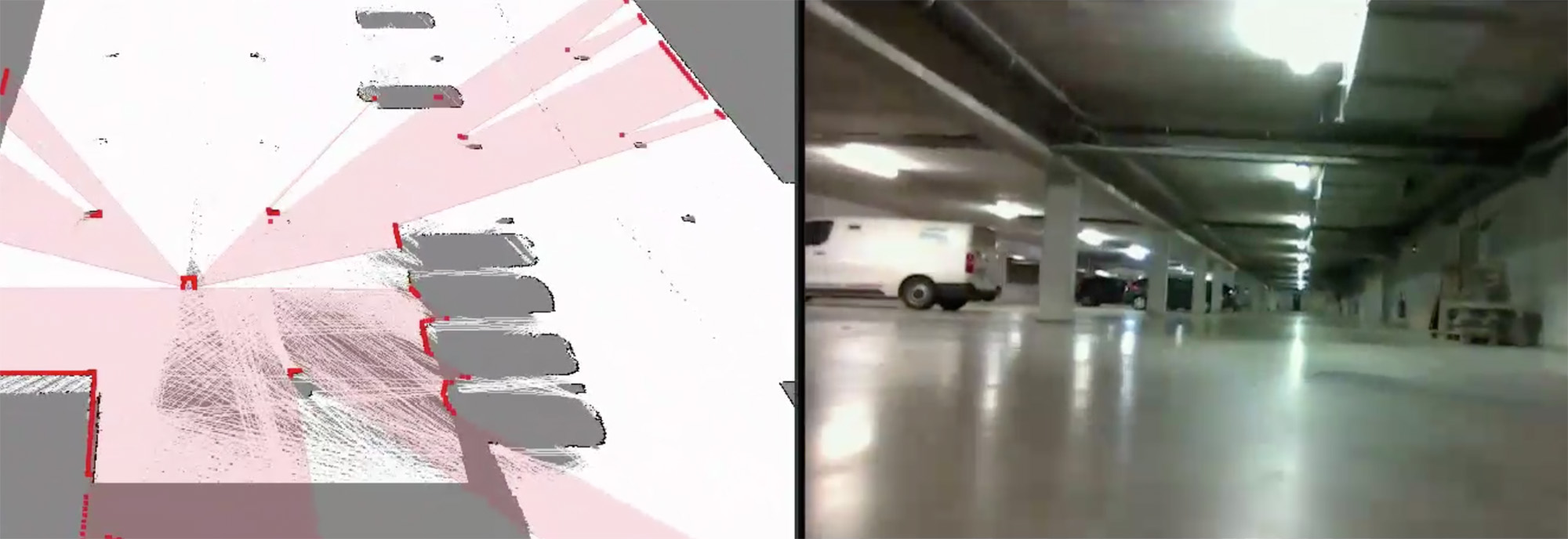